FedEx Dock Maintenance Application
Project Background: With over 600 operational facilities in FedEx’s ground network, sorting packages and getting them to where they need to go is a daunting, finely-tuned process. The Dock Maintenance application is used to configure a facility's dock. The goal is to ensure that packages are unloaded, sorted and successfully routed through the building to the next load point/trailer. Many docks consist of multiple doors, up to 6 shifts per day, and up to 7 days a week. These docks are planned by network planning engineers, who review and plan out the next week's shipments, and implemented by dock staff. The current application was developed 10-15 years ago and is clumsy and inadequate, requiring engineers to rely heavily on spreadsheets.
Problem: How can we improve the process by which engineers plan and implement docks?
Process: Conducted a variety of user research—interviews, contextual inquiries, and facility walkthroughs—with both business and field personnel to better understand their needs. Compared processes with how application owners expected engineers to work, and then mapped out process flows and journey maps for specific tasks. Worked with the business to create low- and high-fidelity prototypes of the ideal experience, which were reviewed and usability tested by engineers and station staff.
Design Solution: Created a new Dock Maintenance application that allows engineers to plan multiple docks, which can be changed easily by station staff during sort. Draft docks function like an engineer’s sandbox, where they can plan out a facility’s future needs. Docks are reviewed and approved, ready for implementation by station staff. Engineers can view assignments inside the application and make and apply changes easily. Future enhancements include automating processes currently handled by spreadsheets and creating an online messaging system to eliminate email.
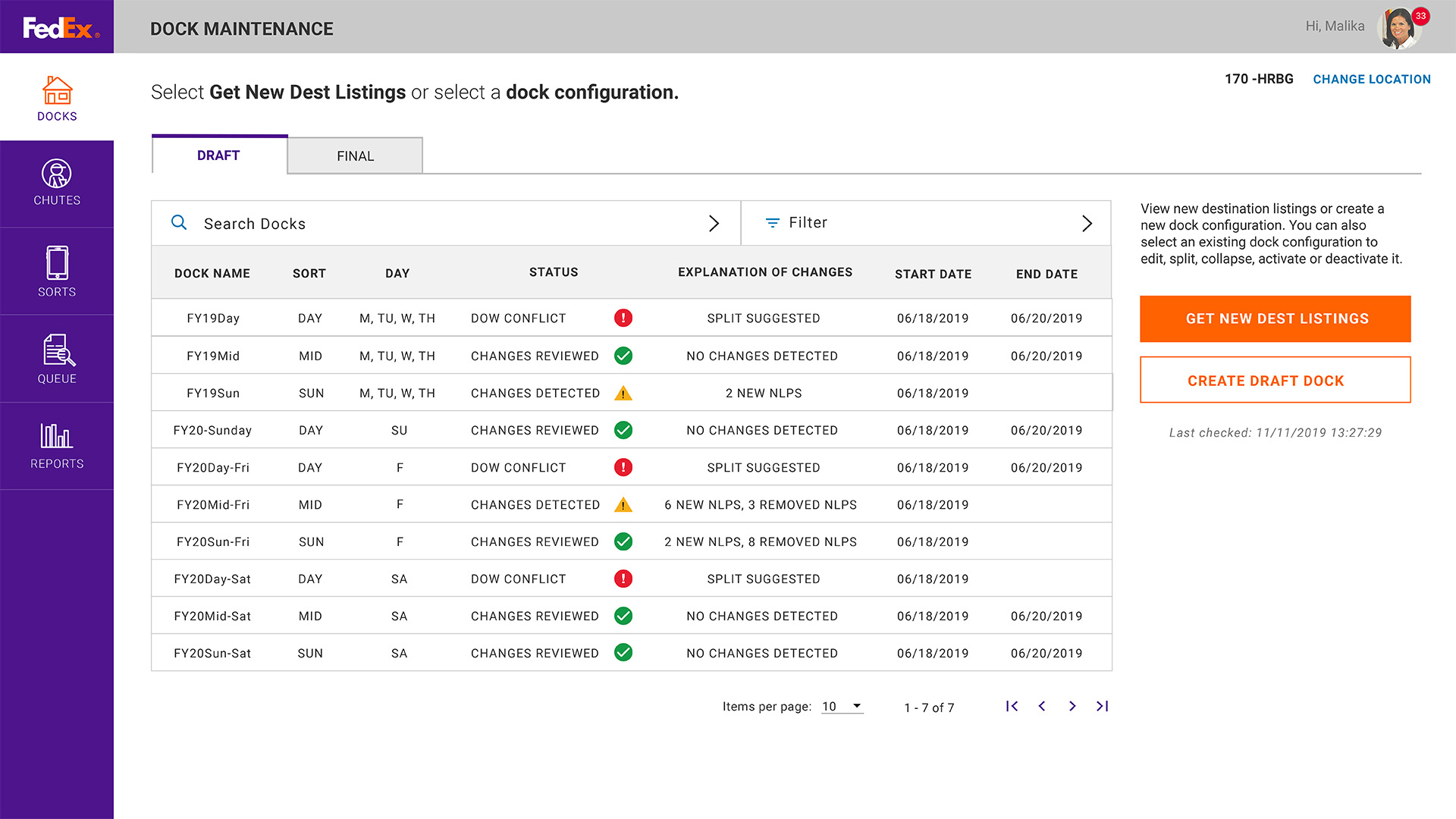
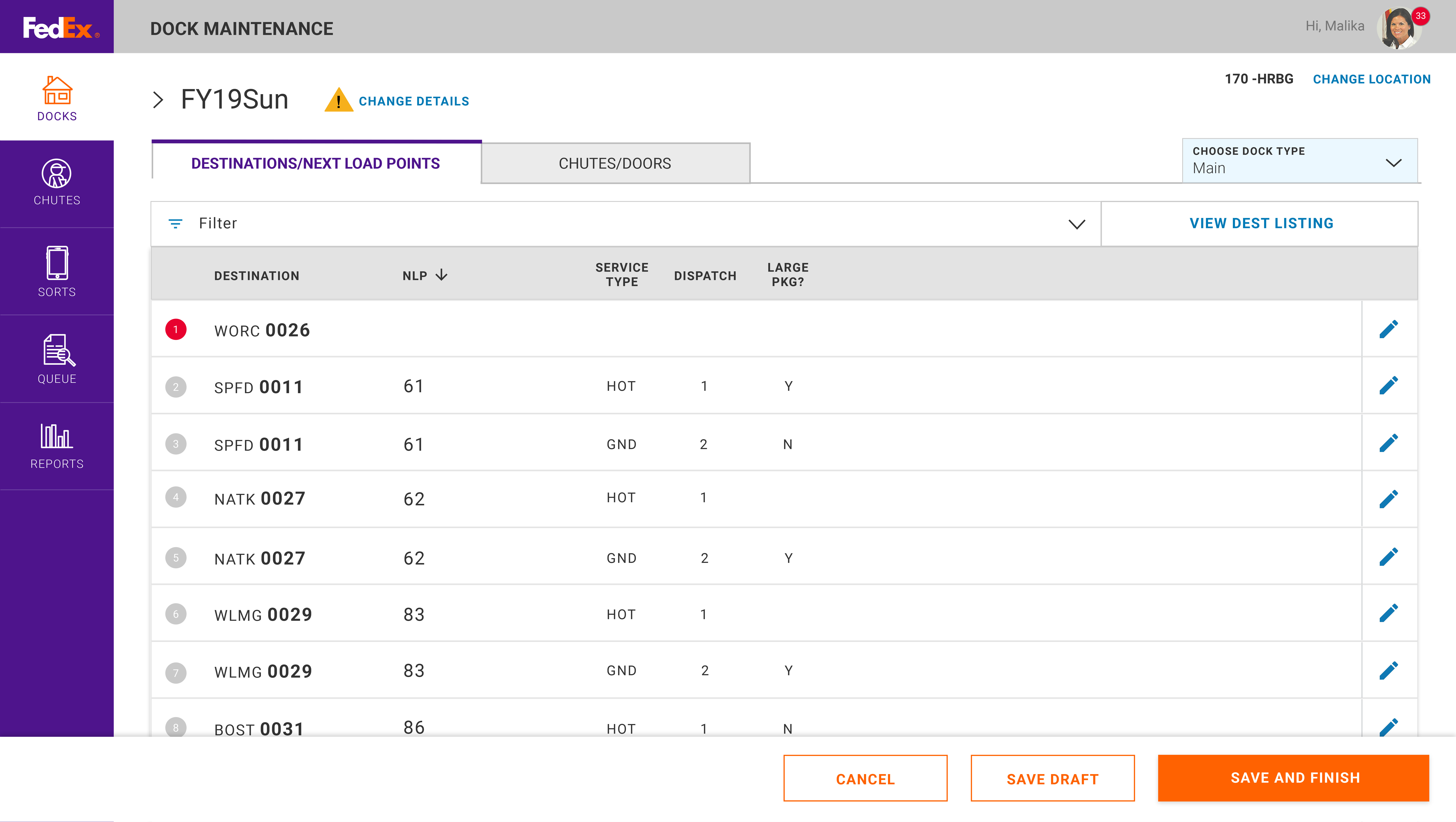